日本富山大学小森幸也等研究人员研究了一种新的加工方法,选择离子铣削来锐化WC (Co)冲头和冲模边缘,增强穿孔中的应力集中,并减少工具磨损和受影响区域的宽度,并发明了激光修整方法作为降低穿孔冲头的顶表面粗糙度和在侧表面上形成纳米纹理,当穿孔厚度为200μm的AISI316L钢板时,受影响区域的宽度显著减小。
在该项研究中,使用了两种类型的氮化SKD11冲头来研究微/纳米织构化对穿孔过程的影响,使用机械研磨的WC(Co)冲头作为参考(表1)。该项工作使用了五块非晶带材叠片,用于分析冲压对穿孔缺陷的影响,并使用扫描电镜和三维轮廓仪测量了影响区宽度和工件表面轮廓。研究发现穿孔冲头的微/纳米织构化是控制穿孔特性和提高穿孔产品质量的关键技术。当使用机械研磨的冲头时,受影响区域的宽度达到非晶带材厚度的三倍以上。此外,施加的功率在裂缝和扭曲的形成中被消耗,以扩大施加的负载-冲程曲线。这拼接孔的直径总是大于冲头的直径;这些缺陷会留在穿孔的板材上;当使用微米/纳米纹理冲头时,受影响区域的宽度显著减小,远小于板材厚度。减小了所施加的载荷与行程的关系,从而降低了冲压时所施加的力的塑性耗散。穿孔直径总是小于冲头直径;这种减少是由穿孔后卸载过程中的回弹造成的;微米/纳米织构取向对上述冲孔工艺是有影响的。当沿着穿孔方向使用微米/纳米纹理冲头时,来自工件的碎屑颗粒被捕获到纳米凹槽中,以将它们从穿孔过程中排出(图2)。通过控制微米/纳米织构的取向,也降低了施加载荷与行程关系中的塑性耗散;由于电机铁心中的铁损是由非晶带材片具有缺陷的残余区域引起的,所以使用微米/纳米纹理冲头的穿孔工艺可以通过最小化受影响区域的宽度来直接减少铁损。特别是,受影响的区域宽度在叠层中的每个非晶片中均匀减小;穿孔质量高,生产率高。因为在这个穿孔过程中允许正常的间隙设置,所以冲头和冲模的寿命得以延长,而不会损失穿孔冲头的质量(图3)。也使得这种微型/纳米纹理工具具有高成本竞争力。
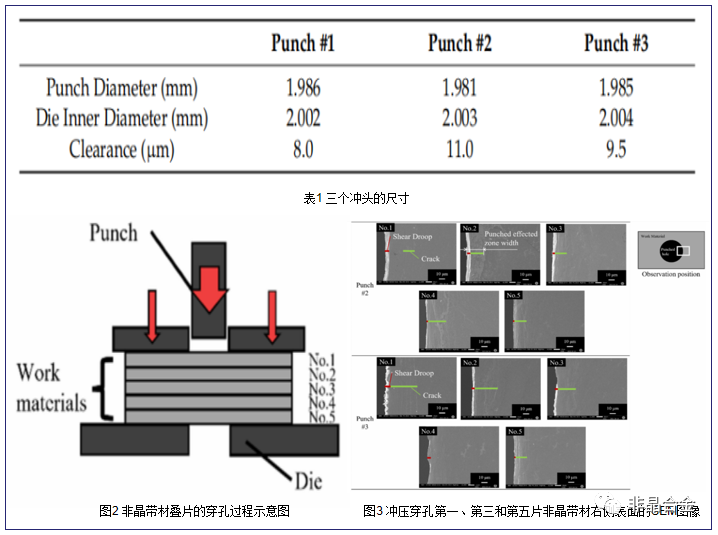