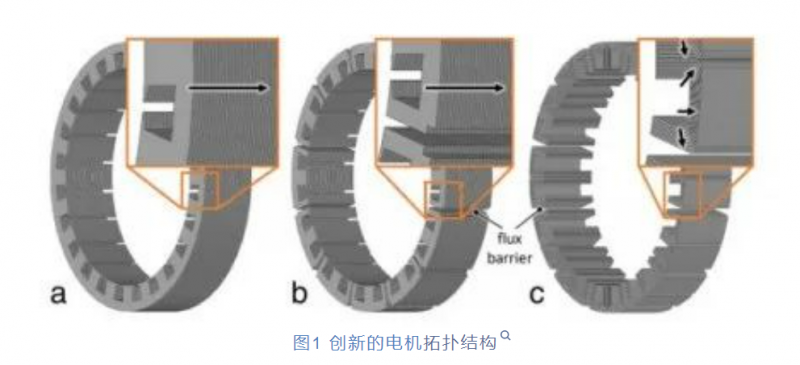
从图1中可以看出,这种创新的电机拓扑结构将经典轴向叠片式铁心结构(图1a)升级为数个单个铁心模块(图1b)组合而成,大小相同的模块式铁心结构可以组成不同外径的定子,这种定子铁心的模块化设计促进了经济而灵活的电机制造,同时也提高了效率。此外为了进一步降低定子铁心的损耗,设计者还把无取向硅钢制作成的轴向叠片铁心模块改换为由取向硅钢制成的径向叠片铁心u型模块(图1c)。这种设计不仅有助于减少涡流损耗,提高电机的效率,还扩大了槽面积,从而可以在槽中放置更多的铜线,进一步提高电机效率。同时,这种设计还通过增加最外层板材的表面积,改善了电机的热管理,使得电机在运行过程中产生的热量可以更有效地散发,提高了电机的可靠性和耐用性。U型铁心模块是通过特殊工艺弯曲加工形成(图2),该工艺主要技术点包括弯曲半径的选择、铁心模块精确制造以及材料的优化利用。这种弯曲工艺和加工可以一次性弯曲10片硅钢片,从而叠片制作成铁心模块,与传统的铁心加工工艺相比,可显著降低刀具成本,工具更加简单灵活,制造成本大幅降低,与传统定子生产材料利用率50-60%相比,新型U型模块式设计的铁心材料利用率可达到95%以上。同时独创的具有旋转夹爪的工具设计,可以温和地处理材料,避免损坏硅钢片表面绝缘涂层,最大程度保护材料性能。
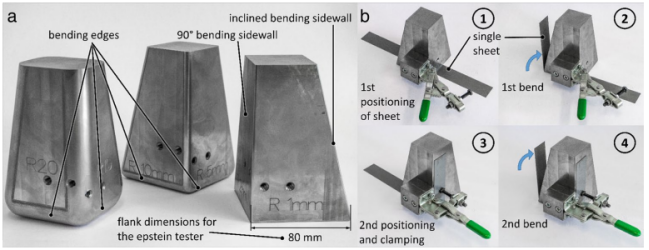
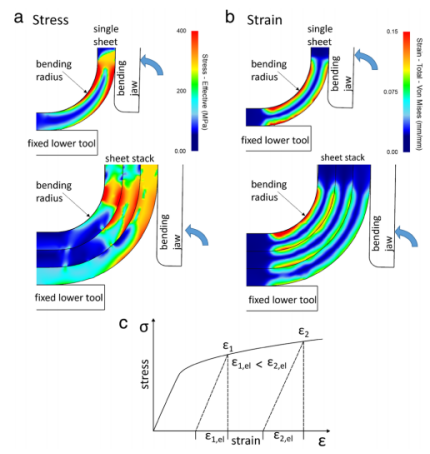
图3 比较单层和3层硅钢片弯曲堆叠成铁心模块后的应力应变分布图;a.应力模拟分布图;b.应变模拟分布图;c.弯曲曲线与回弹的关系
研究人员表示,未来的研究将包括实施完整的制造过程链,减少生产流程,并模块化电机原理应用于其他尺寸的电机。此外,还需要对这种新结构的电机进行详细的性能测试和优化,以确保其在实际应用中的可靠性和效率。